Feedind System To Mining Mill Cement Plant

The Cement Plant Operations Handbook International
2019年4月30日 The Cement Plant Operations Handbook is a concise, practical guide to cement manufacturing and is the standard reference used by plant operations personnel worldwide Providing a comprehensive guide to the entire cement production process from raw material2023年7月11日 • Automated feeding of clinker silos and mill hoppers • Remotecontrolled • Several intermediate discharge points • System length of 400 m and more • Simultaneous Conveying and Storing in the Cement Industry AumundCement mill feeding section facilitates a reliable feeding of clinker, gypsum and other additive like limestone, slag, fly ash etc Mill feeding consists of material hoppers, weighing, conveying to millCement Mill Feeding Cement Plant Optimization2021年10月10日 Cement is made by milling clinker with a mix of grinded gypsum The clinker is produced using a rotary kiln which burns a mixture of limestone, clay, magnesium, silica, and (PDF) Improving Kiln Feed Chemistry and Overburden
.jpg)
Raw Mill Feeding Cement Plant Optimization
After monitoring and controlling the quality of incoming raw material, the area of high activity for quality department to ensure quality mix for smooth production of high quality of cement is “mill feeding system” The system consists of 2024年5月22日 bins to the raw mill An extremely important step in the cement process is to proportionally feed these materials to the raw mill to ensure the correct “blend” of these A practical guide to improving cement manufacturing 2022年9月13日 Weighbelt feeders are crucial throughout multiple stages of cement production, a role that has earned them the title of “the heart of the plant” in the cement industry What are weighbelt feeders and how do they work?Weighbelt Feeders in Cement Production2017年8月26日 The objectives of this study are: (a) to investigate how long the limestone quarry can alone supply the desire quality and quantity materials to the cement plant; and (b) to MINERAL MINING TECHNOLOGY Limestone Quarry
.jpg)
An Optimized Open Pit Mine Application for
2022年11月6日 The two main goals of this paper are to (a) determine how long an operating mine can continue to provide the cement plant with the quality and quantity of materials it needs, and (b) explore the viability of combining some 2024年9月20日 thyssenkrupp Polysius has achieved a major milestone by supplying the proven AFR feeding system prepol® SC to the Sung Shin cement plant, marking the first installation thyssenkrupp Polysius supplies AFR feeding system to Sung Shin cement plantYou've already forked shibang 0 Code Issues Pull Requests Packages Projects Releases Wiki Activityshibang/sbm feedind system to crusher cement plantmd at 2023年8月23日 A cement mill is a fundamental component of the cement manufacturing process, playing a vital role in breaking down and grinding cement clinker into fine powder This finely ground powder, when mixed with other What Are the Parts of a Cement Mills?
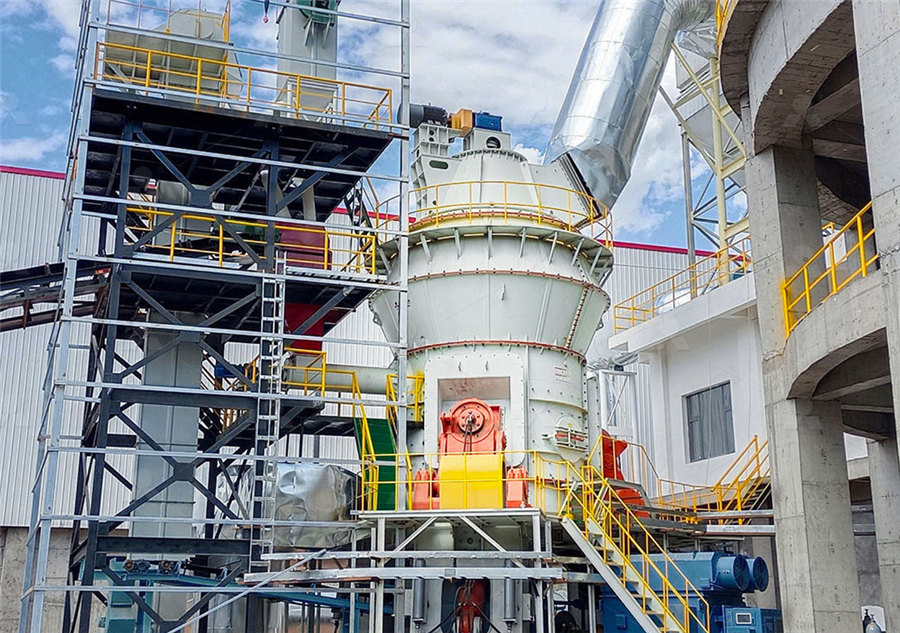
The Cement Plant Operations Handbook International
2019年4月30日 The Cement Plant Operations Handbook is a concise, Emergency power – 12 Plant control systems 6 Cement milling process summary data – 8 Typical equipment downtime 110 1 Storage of clinker and other components – 2 Cement mill specific power consumption – 4 Other systems – 5 Debottlenecking – 6 Project audit – 72019年10月11日 As a cement grinding plant manufacturer, AGICO Cement can provide a cement EPC project as you need We have rich experience in design cement plants and process cement manufacturing machines, such as cement crusher, cement ball mill, cement vertical mill, cement roller press, cement kiln, dryer, clinker cooler, and related cement equipmentCement Grinding Plant Overview Cement Grinding Unit Cement Plant2015年9月6日 This document discusses waste heat recovery (WHR) systems in cement plants It describes how WHR can utilize the industrial waste heat generated during cement production through combined heat and power or cogeneration systems to produce steam or electricity It notes that the rotary kiln in cement plants reaches temperatures of 13002200°C but Waste Heat Recovery System in Cement Plant PPT2024年1月12日 Tushar Kulkarni, Business Head – Minerals, Cement Mining, Siemens Large Drivers India, discusses the role of Artificial Intelligence (AI) and premium efficiency standard products in making cement plant operations more sustainable By FY27, cement consumption in India is expected to reach 45078 million tonnes, driven majorly by expanding demand from Improving Operations using AI Indian Cement Review
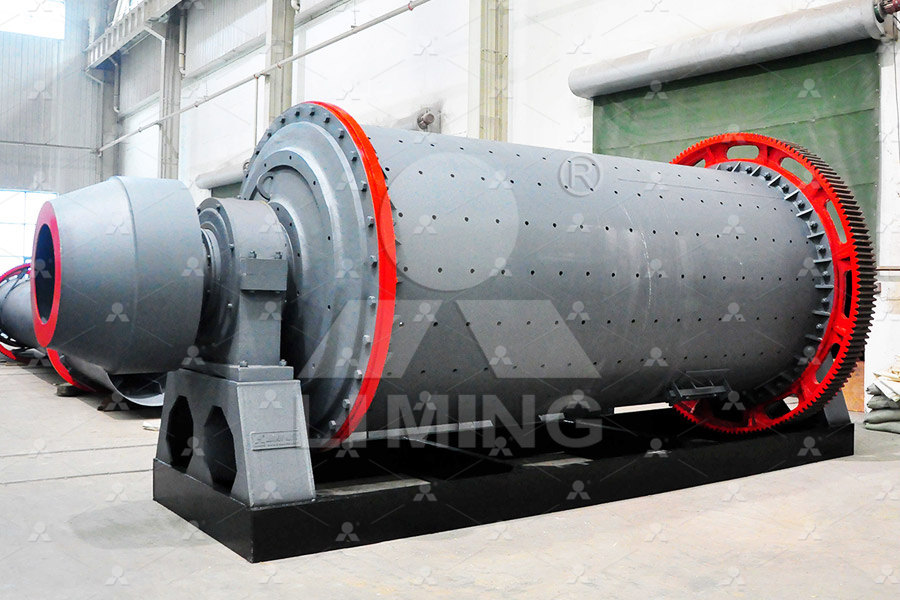
Ball Mill In Cement Plant Cement Ball Mill AGICO Cement
The Closedcircuit Grinding System of Ball Mill in Cement Plant Years of cement production practice shows that cement particle gradation should be distributed continuously within a certain size range Generally speaking, the cement particles smaller than 32 μm are beneficial to reduce bleeding and early strength, but as the size of particles Cemtec Cement and Mining Technology GmbH is a leading manufacturer of dry and wet mills for the cement and mining industry with over 30 years of experience located in Enns/Austria Its portfolio spans from single machines, spare parts and engineering services to the erection and commissioning of turnkey projects in the cement, mining and Energy and cost savings by retrofitting a stateoftheart dry Mill Feeders: Feeders will be directly installed under hoppers with rod gate in between The feeders are generally 2 to 3 m long and discharge on to a common conveyor which will take feed to mill Feeders for mills meter feed rates and also tantalize tons fed For cement mill feeding, table feeders, belt feeders, and weigh feeders have been usedCement Mill Feeding Cement Plant Optimization2017年8月26日 Keywords: Long range planning, cement plant, limestone, mixed integer programming, block aggregation DOI: 101134/S50174 INTRODUCTION The success of cement plant operation is largely depends of the availability of quality raw materials at desire quantity The main raw material for the cement plant is the limestone and theMINERAL MINING TECHNOLOGY Limestone Quarry
.jpg)
How to Start a Cement Factory AGICO Cement
A cement ball mill is ready for transportation There are many kinds of industrial equipment used in a cement plant, including thermal equipment, grinding equipment, dust removal system, transportation system, storage system, and 2024年5月23日 The belt conveyor in cement plant systems provides an efficient and seamless method for transporting materials across various stages of production From handling raw materials like limestone and clay to moving clinker and cement to storage, the belt conveyor in cement plant settings ensures that every phase of cement processing runs smoothly Optimizing Material Flow with Belt Conveyor in Cement Plant2024年10月3日 Cement plant automation enables cement production processes to be carried out more efficiently, enabling cement manufacturers to improve energy efficiency, reduce emissions, and ensure the quality of the produced Cement Plant Automation Rockwell 2019年3月8日 257 HighEfficiency Fans for Cement Mill V ents and focus on specific technical measures that could be implemented by cement plants recovery systems in operation in cement plants TheseIMPROVING THERMAL AND ELECTRIC ENERGY EFFICIENCY AT CEMENT PLANTS

BASIC CEMENT PLANT LAYOUT – Process Cement Forum The Cement
2020年7月4日 14 Cement Mill and Bag House Clinker, along with additives, is ground in a cement mill The output of a cement mill is the final product viz Cement In a cement mill, there is a cylindrical shell lying horizontal which contains metallic balls and as it rotates, the crushing action of the balls helps in grinding the clinker to a fine powder2023年8月21日 • CPI LNVT Ball Mill: CPI LNVT is a renowned manufacturer of grinding equipment for the cement industry Their ball mills are widely used for grinding cement clinker, gypsum and other materials into a fine powder The ball mill operates by rotating a horizontal cylinder, filled with steel balls, which impact and grind the material as it Grinding process is a critical stage in cement production2024年10月3日 Cement plant automation enables cement production processes to be carried out more efficiently, enabling cement manufacturers to improve energy efficiency, reduce emissions, and ensure the quality of the produced cement The PlantPAx® distributed control system (DCS) is a plantwide, scalable, secure and informationenabled process Cement Plant Automation Rockwell Automationleader in mini cement plant solution As a professional mini cement plant manufacturer with rich experience and own factory, AGICO CEMENT can provide specific cement plant project paper covering all aspects, from market analysis, identifying all items like plant and cement equipment, and raw material to forecasting the financial requirements, etc Based on your real needs, we Mini Cement Plant, Small Cement Plant 100700tpd EPC Cement Plant
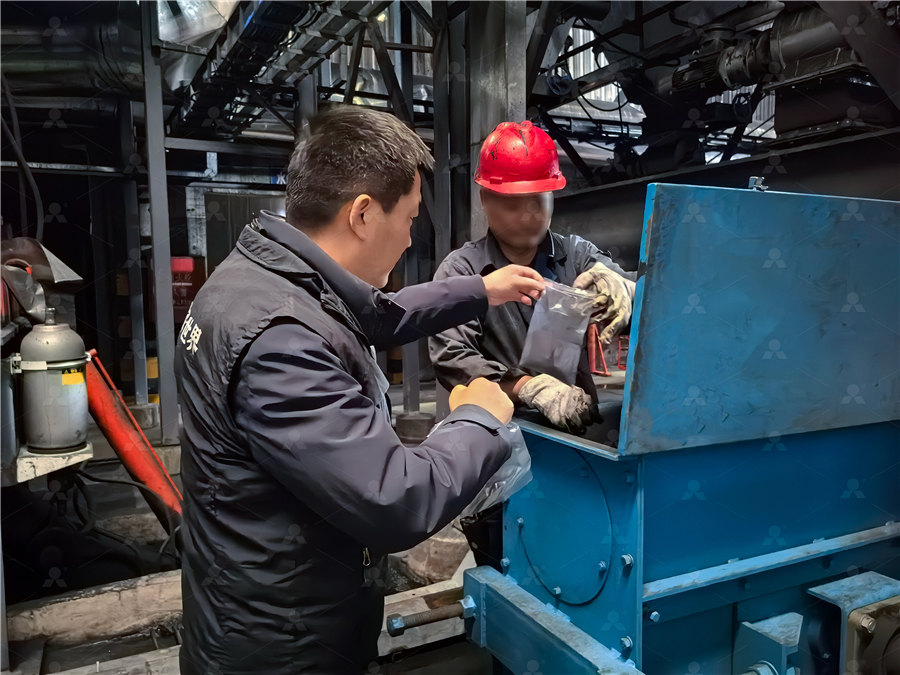
Cement Ball Mill Cost Effective Cement Grinding AGICO Cement Plant
The installation of liners Length Diameter Ratio The lengthdiameter ratio of the cement ball mill is relatively large For mills of opencircuit grinding system, the lengthdiameter ratio is usually between 35 and 6 to ensure that the product fineness is qualified through single grinding; For ball mills in closedcircuit grind system, in order to increase the material flow rate, the length 2021年10月10日 Cement is made by milling clinker with a mix of grinded gypsum The clinker is produced using a rotary kiln which burns a mixture of limestone, clay, magnesium, silica, and iron with desired (PDF) Improving Kiln Feed Chemistry and Overburden3 天之前 That’s why cement plants depend on spray technology and expertise from Spraying Systems Co We’ve worked with cement plants of all sizes all over the world, helping them improve cement quality and productivity while reaching sustainability goals Roll mill Talk to an expert See how you can improve operations in your cement plant with Spray Solutions for Cement Manufacturing Spraying Systems Suitable for raw materials in the cement, coal, pulp and paper, mining and other industries as well as power plants and ports • Both prehomogenisation and buffer storage • FLSmidth have commissioned some of the largest stackers and Everything you need to know about Stacker and
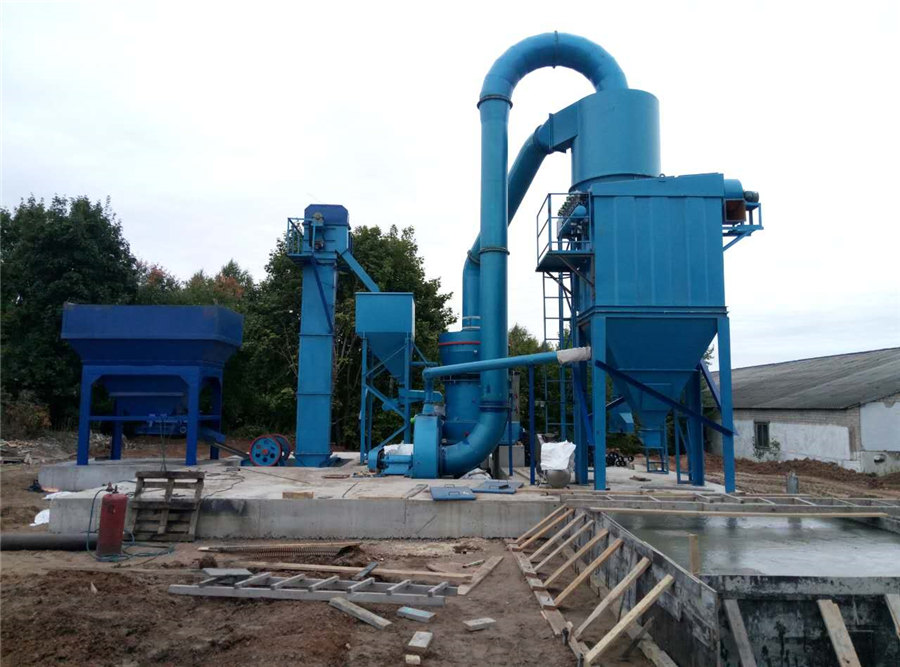
Hydraulic Roller Press in Cement Plants AGICO
The cement roller press is a type of materialcrushing machine which is often used in cement plants It usually works together with a ball mill to form a pregrinding or finalgrinding system for the grinding of raw materials, coal, and AGICO CEMENT is a cement plant manufacturer supplies cement equipment with high quality and competitive price, including cement mill, cement kiln, cement crusher, and other cement plant equipment any need? Skip to content +86 s about blog contact EN ES MenuCement Equipment, Cement Plant Equipment Cement Plant Contribute to brblmd/sbm development by creating an account on GitHubsbm/sbm feeding system to cement crusher plantmd at 6 Cement Mill The cement mill grinds the clinker to a fine powder, which is then mixed with gypsum to form cement Equipment: Ball mills, vertical roller mills Technical Specifications: Ball Mills: 1030 tons/hour capacity, 5001500 kW motor power Vertical Roller Mills: 2050 tons/hour capacity, 10003000 kW motor power Example Brands:The Comprehensive Guide to Cement Plant Costs: An In
.jpg)
Modular grinding plant Mill system ready2grind Gebr
Pfeiffer’s modular mill solution enables flexible use in any place, bringing cement producers closer to their customers This compact system is suited to producing all types of cement – perfect for local cement producers and market entrants as well as for large construction companies aiming to expand their position by manufacturing cement on the spotDevelopment of a feeding system for a roller mill, which has a hopper and a 12m conveyor belt that feed the mill includes plan and elevation Chilean mining mill dwg 314 Ball mill block for mining dwg 16k Flotation cell for concentrates dwg 15k Side boom plant and pipeline elevation dwg 26k Load more Content Library Feeding system to a mill in AutoCAD Bibliocad2019年1月3日 Clinker grinding technology is the most energyintensive process in cement manufacturing Traditionally, it was treated as "low on technology" and "high on energy" as grinding circuits use more than 60 per cent of total energy consumed and account for most of the manufacturing cost Since the increasing energy cost started burning the benefits significantly, Clinker grinding technology in cement manufacturingIn a cement plant, a cement roller press is a kind of important cement equipment used for clinker grinding It is usually combined with a cement ball mill to form a highefficiency cement grinding system because the practice shows that the grinding process with a small grinding ratio and stepbystep completion is more energysaving than that Cement Roller Press Roller Press In Cement Plant Roller
.jpg)
shibang/sbm feedind system to crusher cement plantmd at
You've already forked shibang 0 Code Issues Pull Requests Packages Projects Releases Wiki Activity2023年8月23日 A cement mill is a fundamental component of the cement manufacturing process, playing a vital role in breaking down and grinding cement clinker into fine powder This finely ground powder, when mixed with other What Are the Parts of a Cement Mills?2019年4月30日 The Cement Plant Operations Handbook is a concise, Emergency power – 12 Plant control systems 6 Cement milling process summary data – 8 Typical equipment downtime 110 1 Storage of clinker and other components – 2 Cement mill specific power consumption – 4 Other systems – 5 Debottlenecking – 6 Project audit – 7The Cement Plant Operations Handbook International 2019年10月11日 As a cement grinding plant manufacturer, AGICO Cement can provide a cement EPC project as you need We have rich experience in design cement plants and process cement manufacturing machines, such as cement crusher, cement ball mill, cement vertical mill, cement roller press, cement kiln, dryer, clinker cooler, and related cement equipmentCement Grinding Plant Overview Cement Grinding Unit Cement Plant
.jpg)
Waste Heat Recovery System in Cement Plant PPT
2015年9月6日 This document discusses waste heat recovery (WHR) systems in cement plants It describes how WHR can utilize the industrial waste heat generated during cement production through combined heat and power or cogeneration systems to produce steam or electricity It notes that the rotary kiln in cement plants reaches temperatures of 13002200°C but 2024年1月12日 Tushar Kulkarni, Business Head – Minerals, Cement Mining, Siemens Large Drivers India, discusses the role of Artificial Intelligence (AI) and premium efficiency standard products in making cement plant operations more sustainable By FY27, cement consumption in India is expected to reach 45078 million tonnes, driven majorly by expanding demand from Improving Operations using AI Indian Cement ReviewThe Closedcircuit Grinding System of Ball Mill in Cement Plant Years of cement production practice shows that cement particle gradation should be distributed continuously within a certain size range Generally speaking, the cement particles smaller than 32 μm are beneficial to reduce bleeding and early strength, but as the size of particles Ball Mill In Cement Plant Cement Ball Mill AGICO CementCemtec Cement and Mining Technology GmbH is a leading manufacturer of dry and wet mills for the cement and mining industry with over 30 years of experience located in Enns/Austria Its portfolio spans from single machines, spare parts and engineering services to the erection and commissioning of turnkey projects in the cement, mining and Energy and cost savings by retrofitting a stateoftheart dry
.jpg)
Cement Mill Feeding Cement Plant Optimization
Mill Feeders: Feeders will be directly installed under hoppers with rod gate in between The feeders are generally 2 to 3 m long and discharge on to a common conveyor which will take feed to mill Feeders for mills meter feed rates and also tantalize tons fed For cement mill feeding, table feeders, belt feeders, and weigh feeders have been used2017年8月26日 Keywords: Long range planning, cement plant, limestone, mixed integer programming, block aggregation DOI: 101134/S50174 INTRODUCTION The success of cement plant operation is largely depends of the availability of quality raw materials at desire quantity The main raw material for the cement plant is the limestone and theMINERAL MINING TECHNOLOGY Limestone Quarry